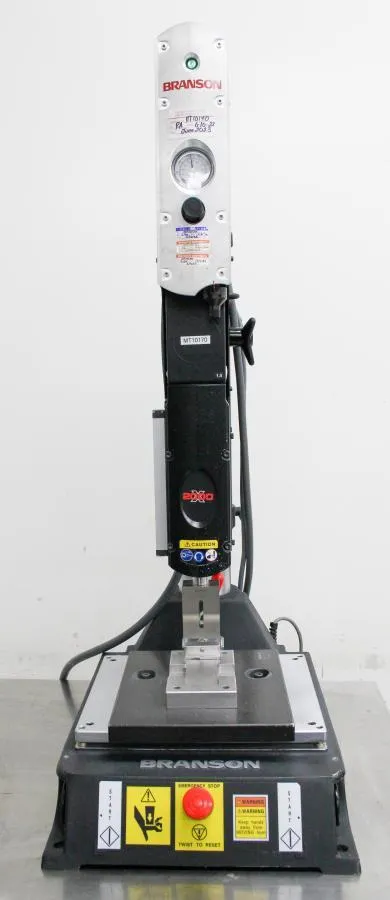
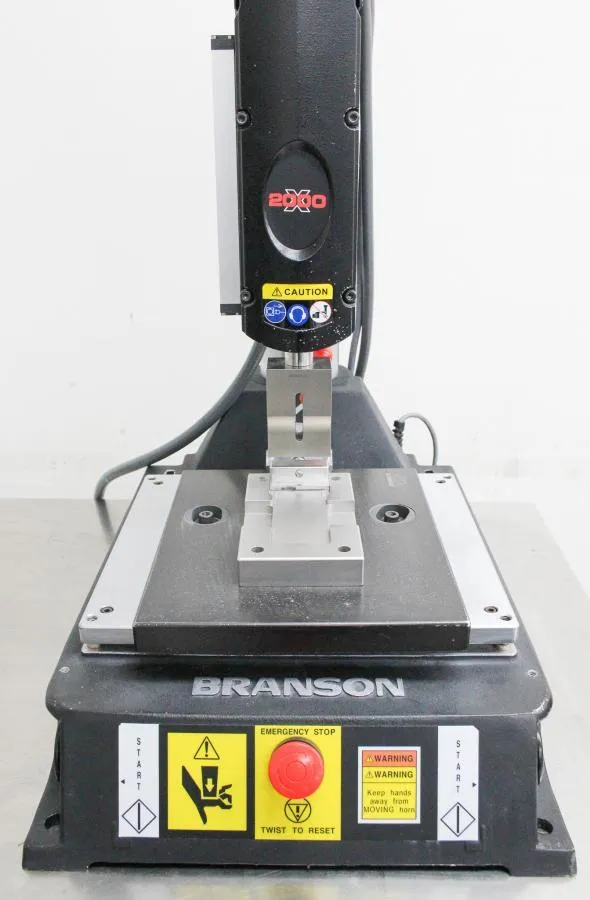
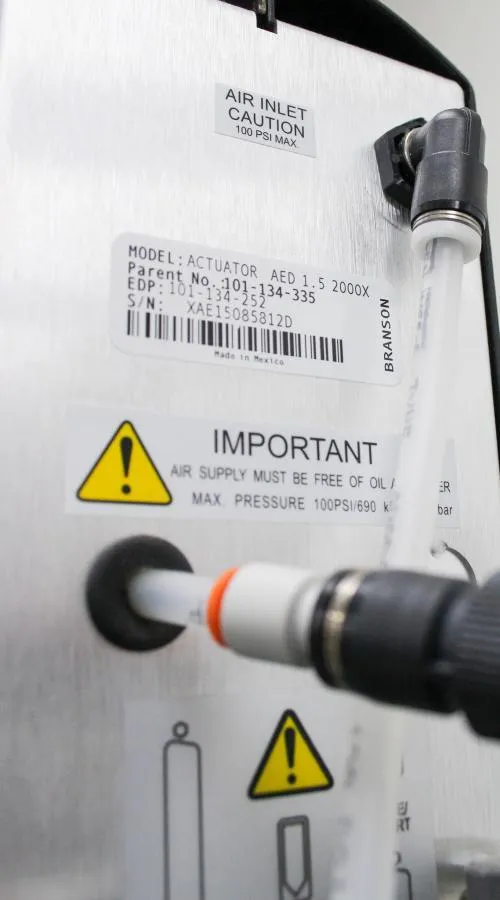
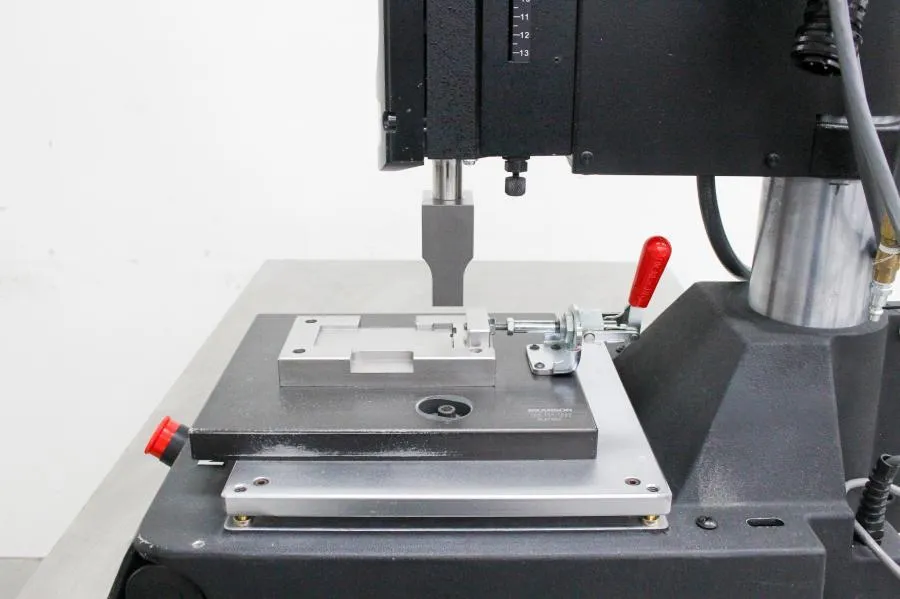
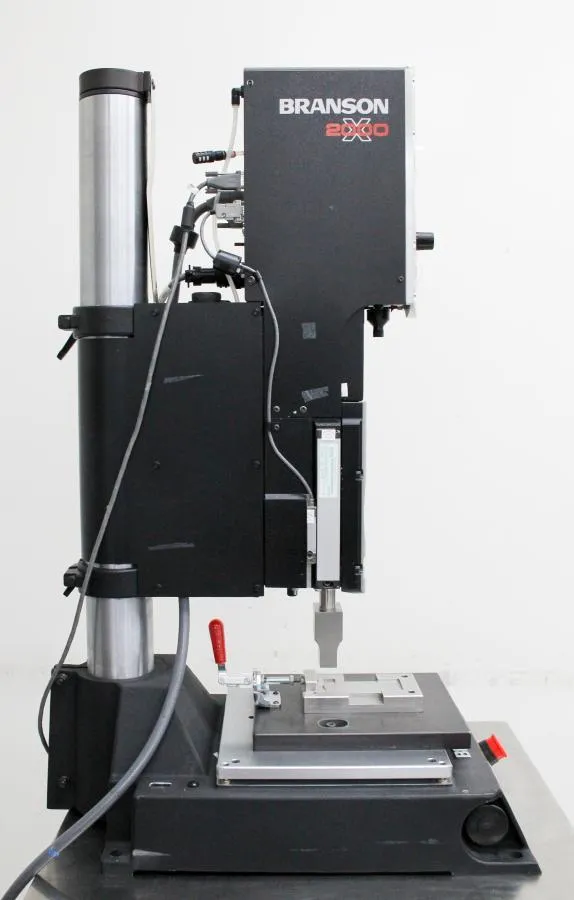
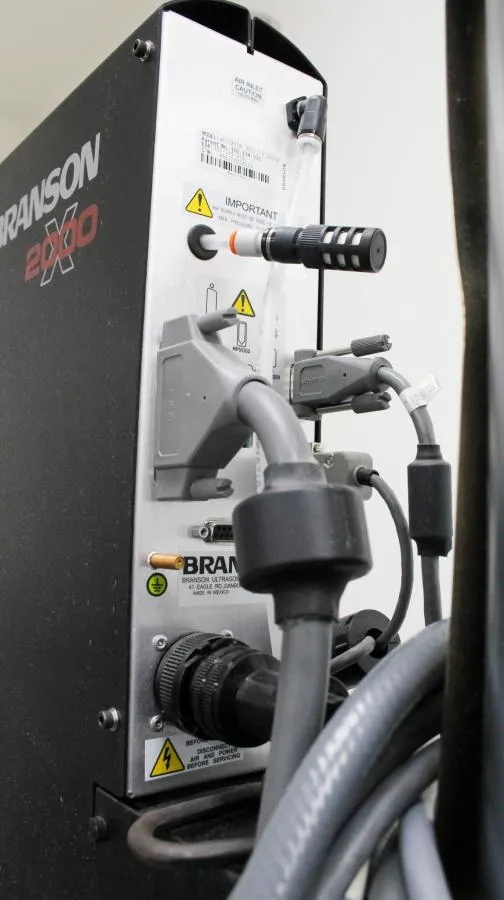
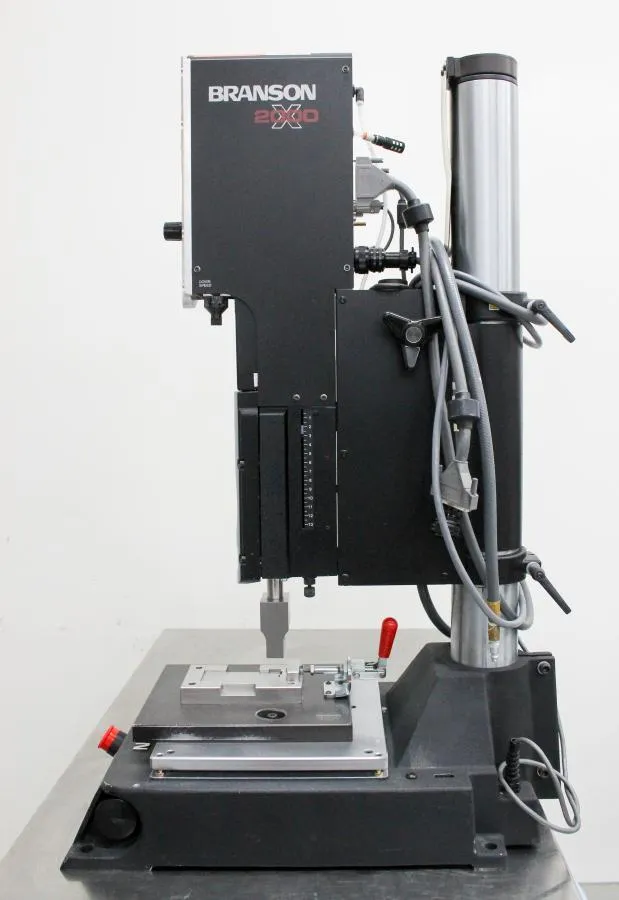
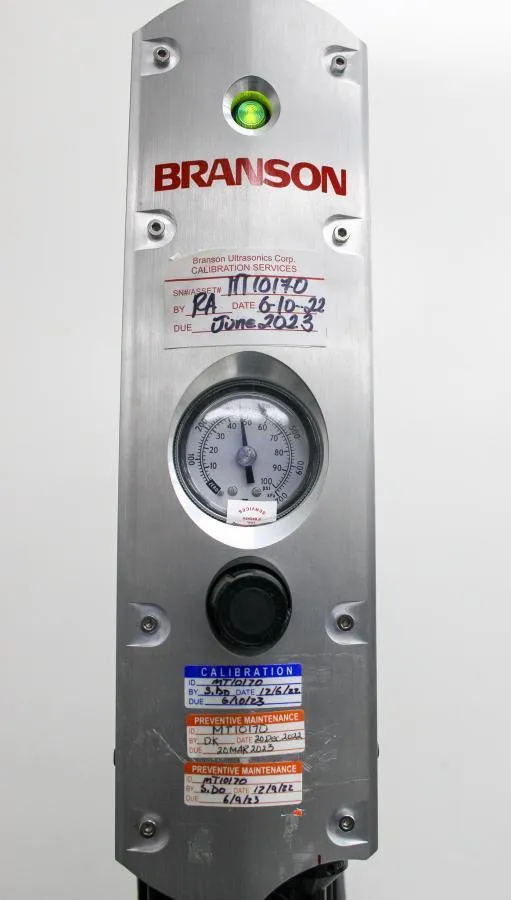
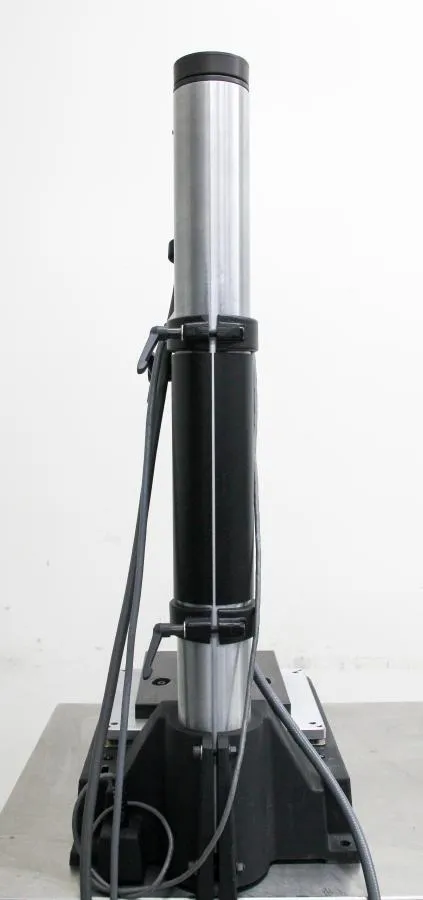
Branson - Actuator AED 1.5 2000X Series Ultrasonic Welder
- Make Branson
- Model Actuator AED 1.5 2000X
- Serial XAE15085812D
- Weight 280
- Working Working
- Warranty 30-Day Warranty, 100% Parts and Labor
- Dimensions 33×22×51 in
- Shipping Type Freight
- Item Condition Pre-owned
Branson Actuator AED 1.5 2000X Series Ultrasonic Welder
***Actuator was tested to specifications. Unit is preowned with minimal wear from normal use. (Note: Does NOT include XDT power supply, E stop is loose.) 30-day warranty included with purchase. See photos for details.
The 2000X aed Actuator is a compact, rigid unit designed for use in manual, semi-automated, and automated ultrasonic welding systems. The Actuator can be mounted directly on an I-beam (or similar machine frame), or it can be mounted on a column and base with start switches and used in a manual or benchtop system. The Actuator is designed to be operated in an upright position, but is capable of running horizontally or inverted. If you are mounting your equipment in an inverted position.
The 2000X aed Actuator requires a 2000X distance Power Supply for power and control of the Actuator’s operation and to provide ultrasonic power to the Converter in the Actuator.
The 2000X aed Actuator is designed with full, built-in pneumatic controls, and mechanical controls. Operation of the 2000X aed is controlled by inputs to the 2000X distance Power Supply.
Ultrasonic Plastics Welding
Thermoplastic parts are welded ultrasonically by applying high-frequency vibrations to the parts being assembled. The vibrations, through surface and intermolecular friction, produce a sharp rise in temperature at the welding interface. When the temperature is high enough to melt the plastic, there is a flow of material between the parts. When the vibrations stop, the material solidifies under pressure and a weld results.
The Plastics Welding System
The welding system consists of a power supply, an actuator, and a converter-booster-horn stack. The system can perform a variety of ultrasonic welding operations, including: inserting, staking, spot welding, swaging, degating, and continuous operations. It is designed for use in automated, semi-automated, and/or manual production systems.
Features:
- Amplitude Stepping: A patented Branson process, controlled by the Power Supply. At a specified time, energy, peak power, distance, or by external signal you can change the amplitude during the weld to control the flow of plastic. This feature helps ensure part consistency, higher strength parts and control of flash.
- Digital Horn Test Diagnostics: In Test mode of the Power Supply, you can view the Horn Test results in digital form, using digital readouts and bar graphs on the Power Supply to give you the best picture of the stack’s operation.
- Pretrigger: This feature allows you to set the system weld controls to turn the ultrasonics on before contact with the part.
- Afterburst: This feature allows you to set the system weld controls to turn the ultrasonics on after the weld and hold steps to release parts from the horn.
- Control Limits: With some power supply models, these secondary controls are used in conjunction with the main parameters of the weld parameters. These user programmed limits provide for adaptive control of the weld process.
- Process Alarm Display Showing Actual and Set Values: When an alarm condition has occurred, you can view the value for the last weld and the suspect and reject settings you programmed into the controls.
- Post Weld Seek: This system feature provides a short burst of energy at the end of the weld Hold and Afterburst steps to automatically retune the power supply, if required.
- Frequency Offset: This process feature allows a user to set a frequency value, for certain specific applications, where the force imparted on the fixture or anvil causes a frequency shift in the Stack’s operation. You should only use this feature when advised to do so by Branson.
- English (USCS)/Metric Units: This feature allows the welder to be set up in the local units in use.
- Startup Diagnostics: At power supply startup, the controls test the major system components, including the Actuator and its controls.
- Weld Parameter Entry through Digital Keypad: User Setup is direct and easy, by selecting the menu parameter by name and using the keypad to enter the precise value. The controls also support entry by incrementing existing values.
- System Information Screen: This is a screen that will give you information about your welding system (e.g., cylinder size, stroke length, number of cycles). Refer to this screen when contacting Branson for service and support.
- Ramp Starting: The starting of the 2000X-series power supply and horn is done at the optimum rate to reduce electrical and mechanical stress on the system. This also helps make some tough-to-start applications possible.
- True Wattmeter: The controls on the power supply include a true wattmeter for accurate measurement of power and energy.
- S-Beam Load Cell/Dynamic Follow Through: The load cell allows the ultrasonics to be triggered at a designated force input into the power supply.
- Encoder: Allows the power supply to monitor the distance the horn has travelled, enabling the use of distance functions.
- Downspeed: Controls the rate of descent and force build-up on the part.
- Pressure Sensor: Allows the power supply to read the system pressure.
Testimonials
“REUZEit has been a great partner for our used equipment needs and always provide timely updates of new arrivals of consigned equipment.”
“Great company to work with. Tammy completed our first international equipment shipment with ease.”
“Fast response, open to adjusting schedule as needed, and great customer interaction.”